3D Printing
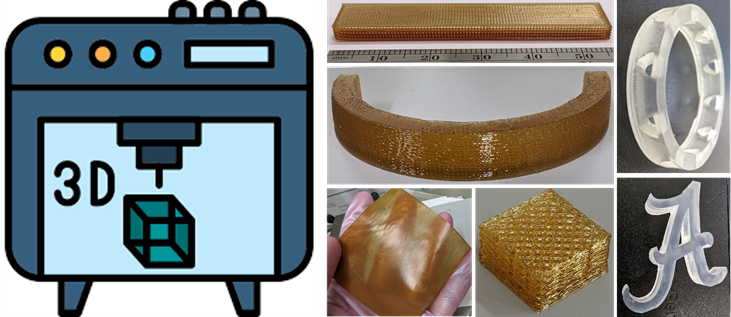
3D printing is an exciting additive manufacturing process whereby material is built layer-by-layer to create any complex 3D structure in a precise manner, subsequently creating less material wastage, unlike other subtractive or mold manufacturing processes. 3D printing involves designing a 3D model of a desired object with the help of computer-aided design (CAD) programs such as Autodesk Fusion 360 or Solidworks, converting it to a language that the 3D printer understands e.g. a standard tessellation language (STL) or an additive manufacturing file (AMF) mesh format, and finally feeding it to the 3D-printer to print the object. Bara’s group deals with fused deposition modeling (FDM) and stereolithography (SLA) 3D printing technology. FDM printers build parts by extruding melted plastic onto the build plate one layer at a time, while SLA printers build parts by polymerizing a liquid photopolymer resin with a UV laser one layer at a time. The raw feedstock materials supplied to the FDM and SLA 3D printers can be plastic filaments, wires, polymer powders, or liquid photopolymer resins. In addition to conventional FDM 3D printers, Bara lab has a pressure-extrusion-based FDM printer (3D Bioplotter from Desktop Metal) which takes the powdered solid feedstock material to 3D-print several compact and porous geometrical structures (with or without additives) such as cubes, slabs, discs, customized complex shapes and so on. 3D Bioplotter is capable of extruding fibers and 3D-printing objects from room temperature to 250 °C. 3D-Bioplotter was used to 3D-print and validate the functionality of several polymers, and their composites and test their performances such as tensile strength, elasticity, and self-healing abilities. The SLA printers were used for applications wherein the plastics such as PVC were upcycled to improve the flexibility of the ABS-like 3D-printed parts while maintaining the required tensile strength.